Thanks for your business!
Category Archives: Jobs
Job 17 – Fossil Watch Battery Replacement
Job 16 – Coach Watch Battery Replacement
Job 8 – Sony a7iii Repair
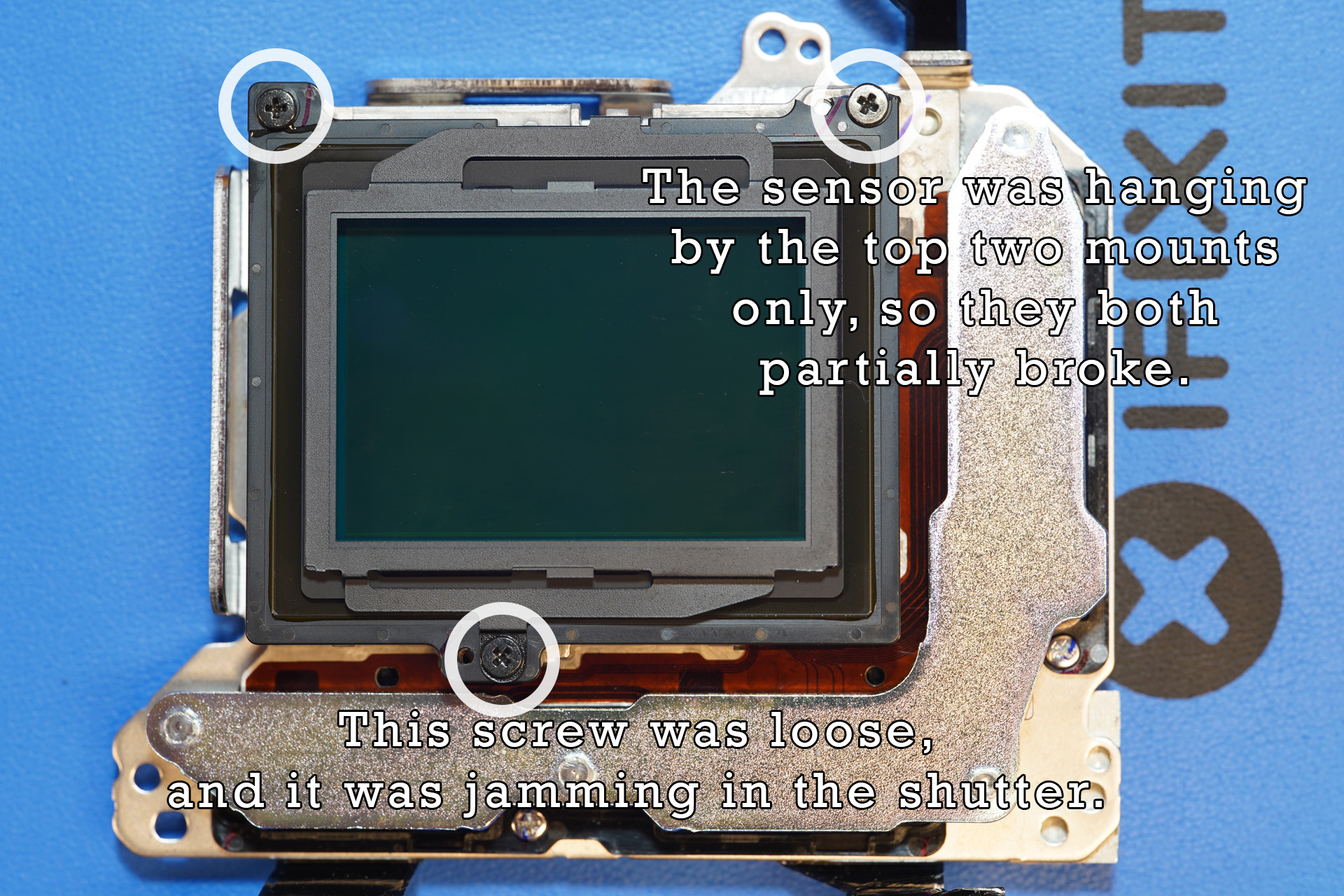
I disassembled and repaired my own Sony a7iii and wrote this disassembly guide on the iFixIt site:
https://www.ifixit.com/Guide/Sony+a7iii+Disassembly/166520
I want to promote my iFixIt guide, but I should be honest, I followed this video when I did mine. Click here.
Job 7 – Elgin Pocket Watch
Watch Model: Elgin National Watch Company (619485?)
Movement Serial Number: Elgin National Watch Company 8739946
Mass: 58.3g
Case Outer diameter: 42.0mm
Crystal diameter:
Thickness: 11.7mm
Movement Dimensions:
https://pocketwatchdatabase.com/search/result/elgin/8739946
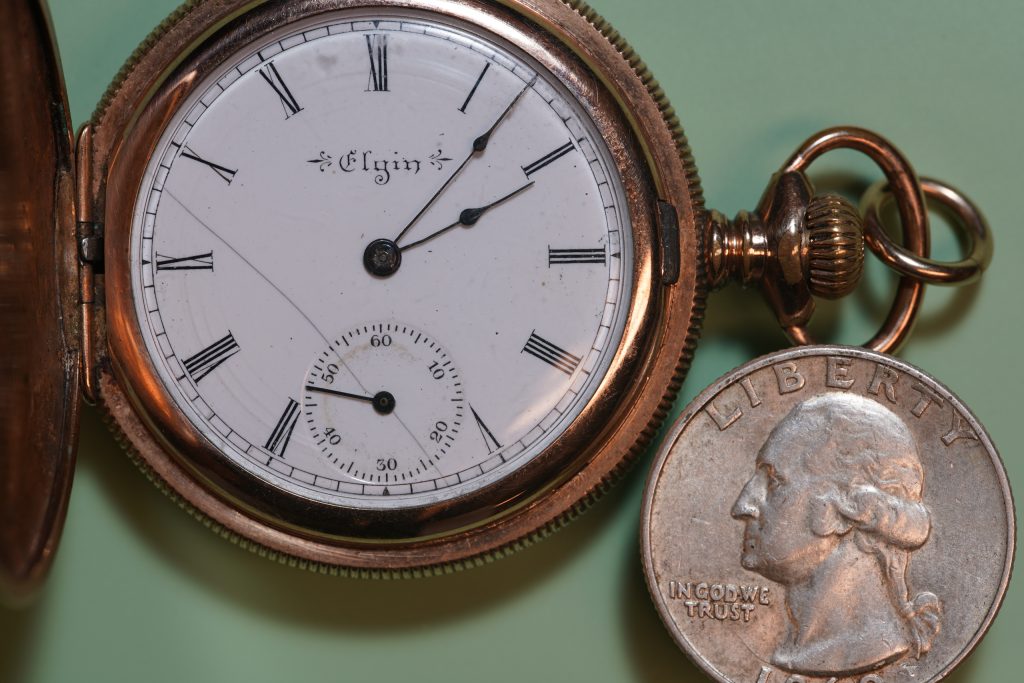
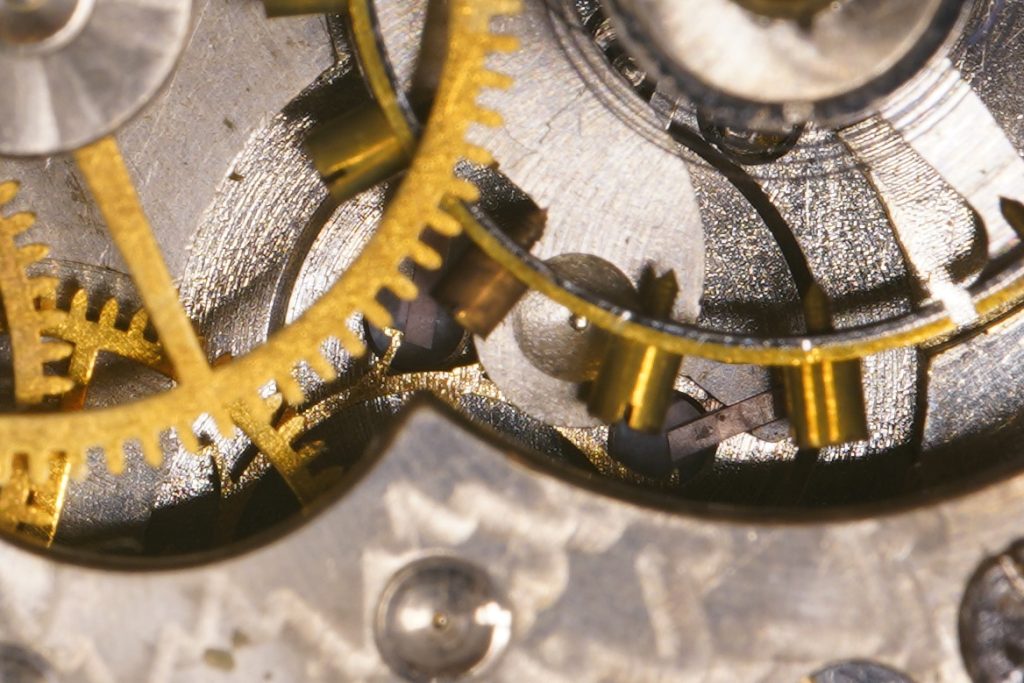
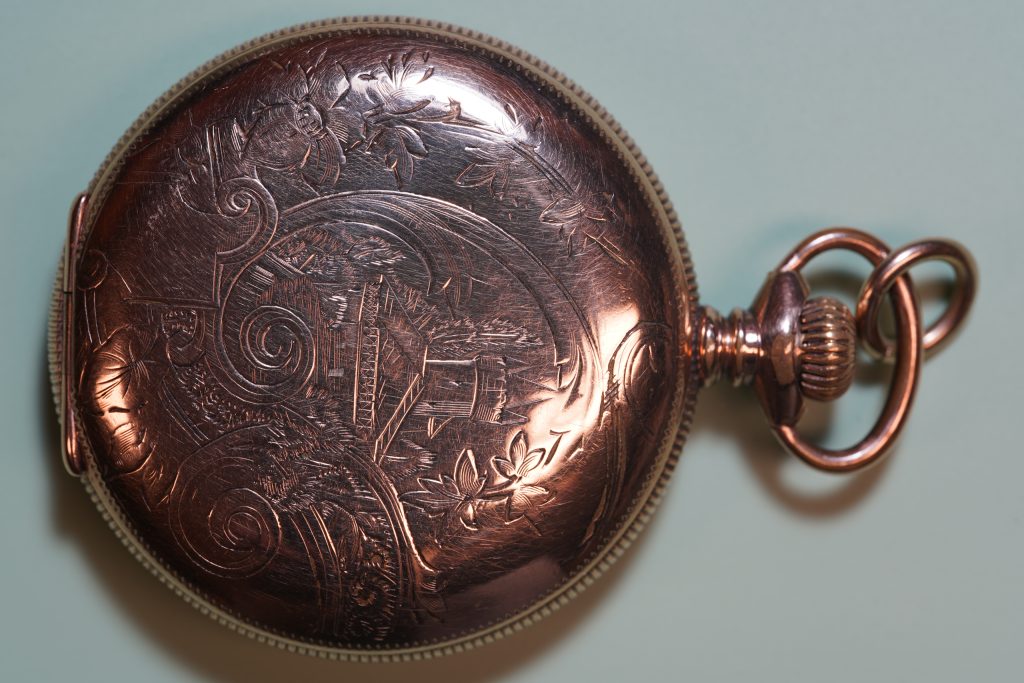
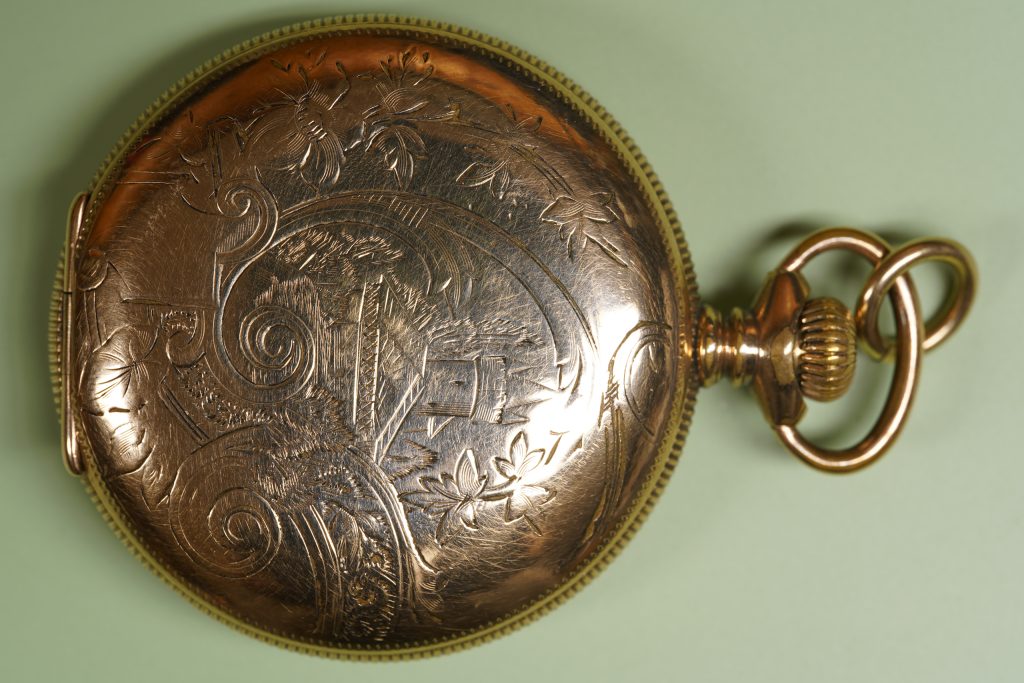
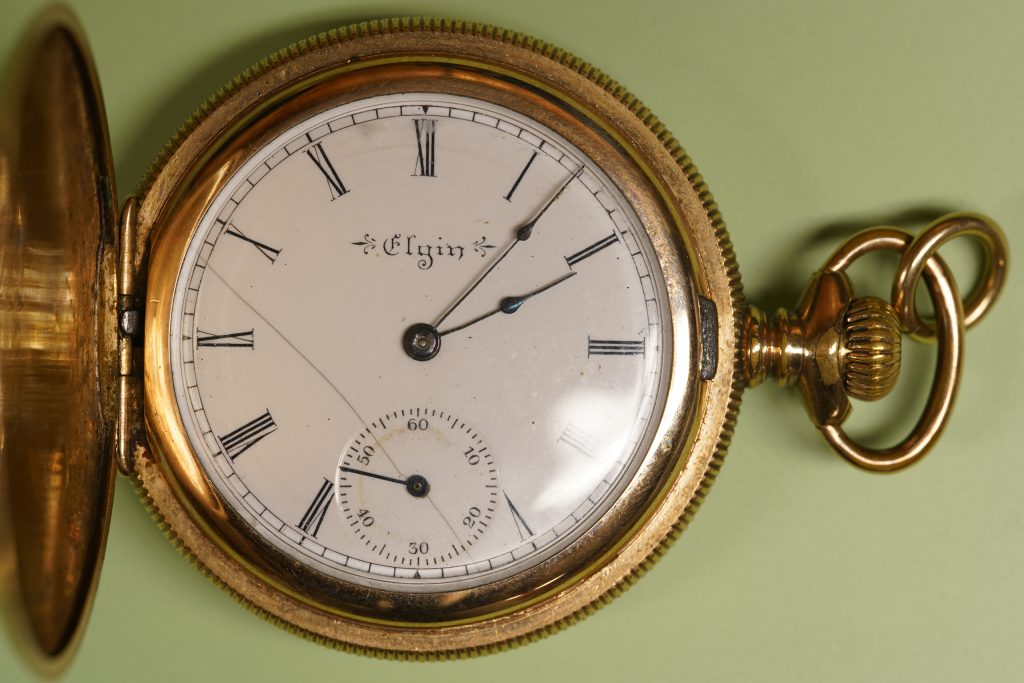
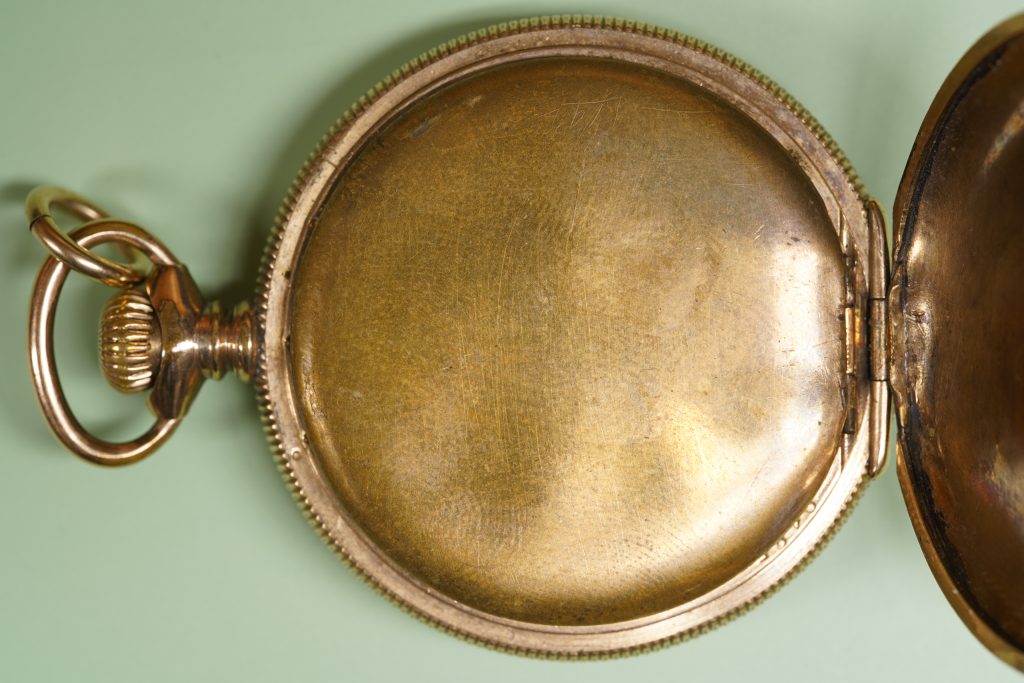

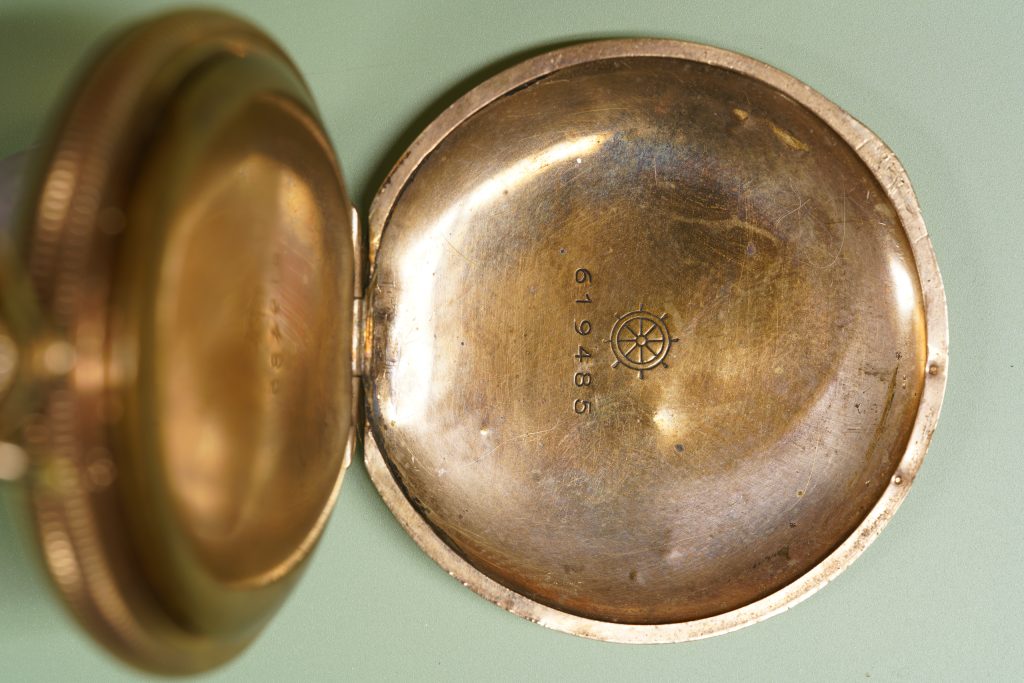
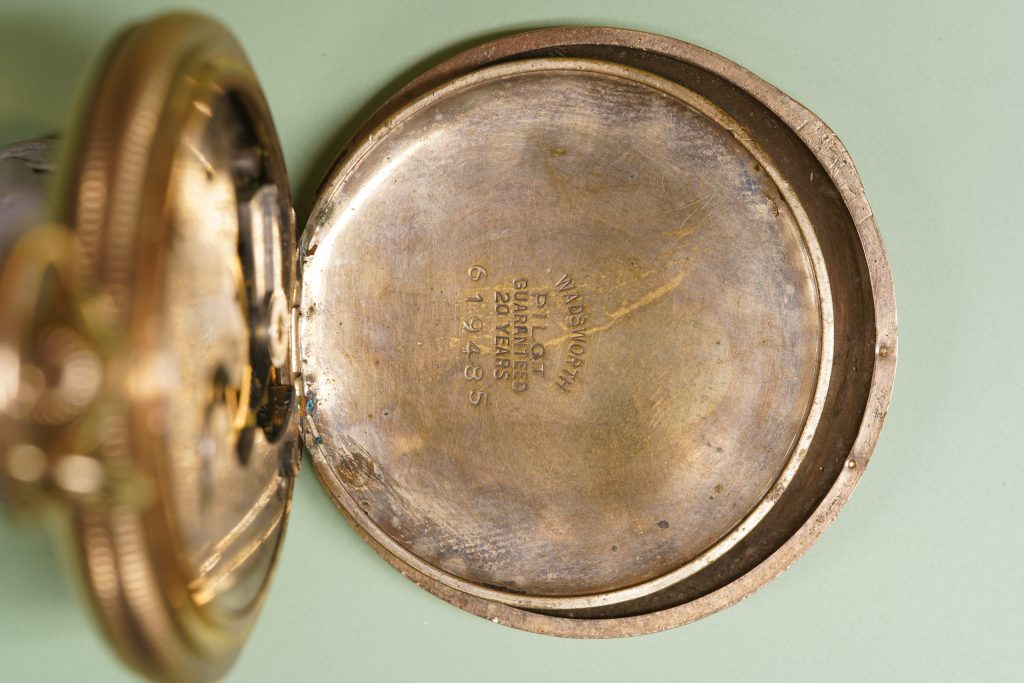

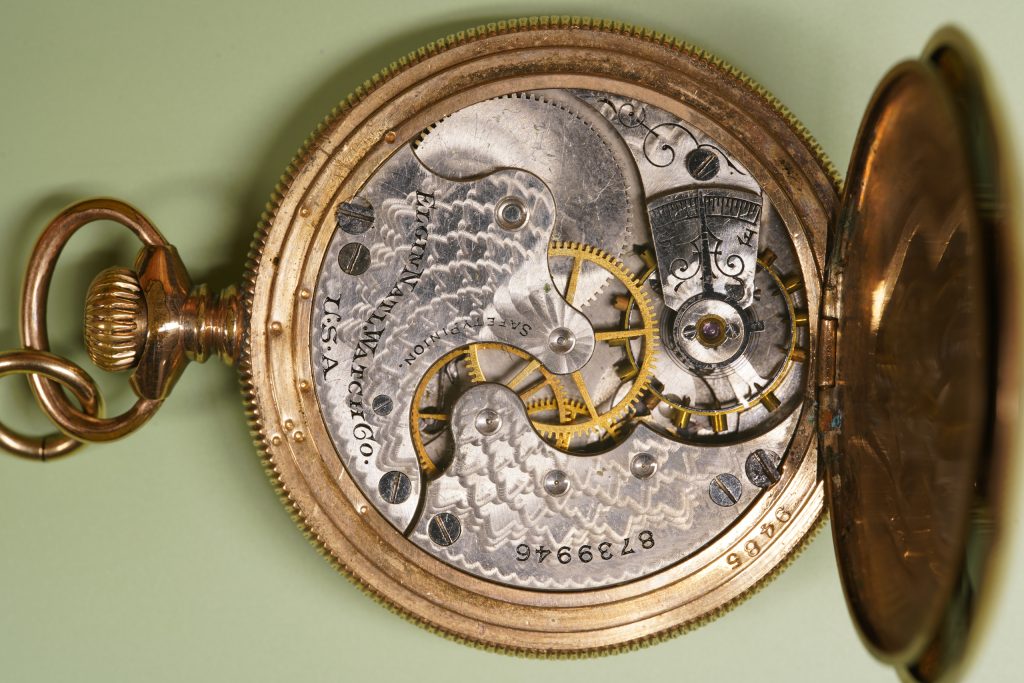
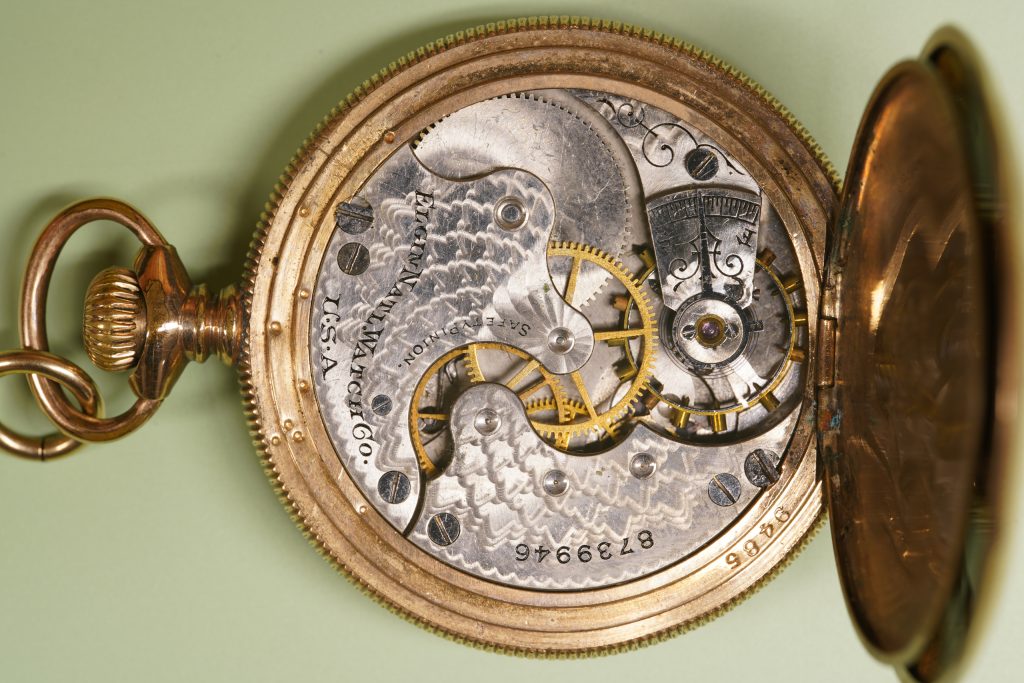
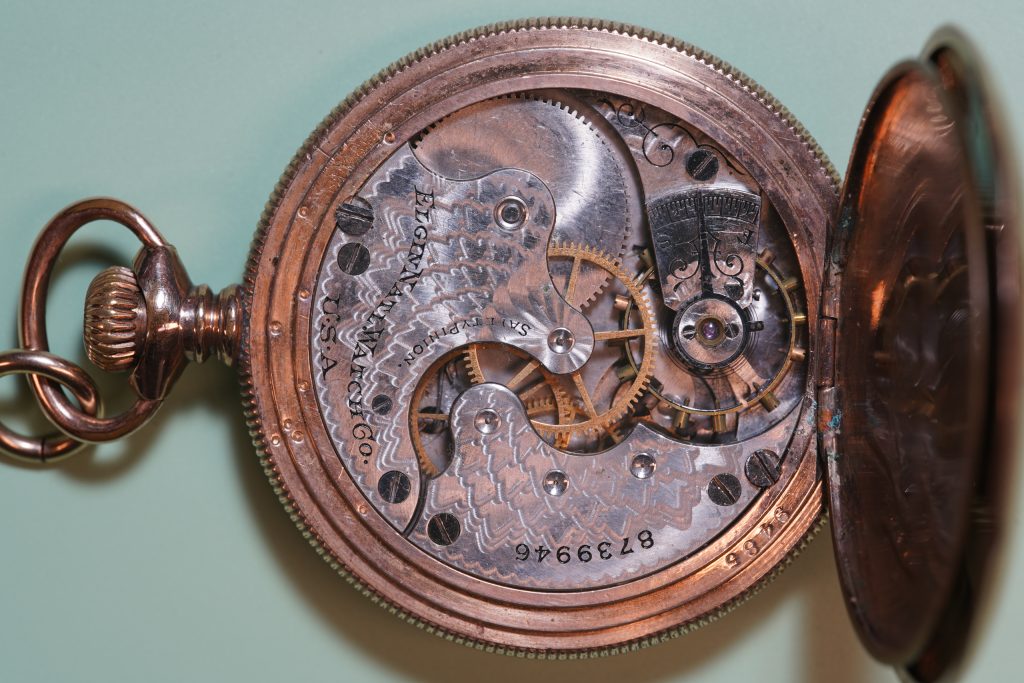
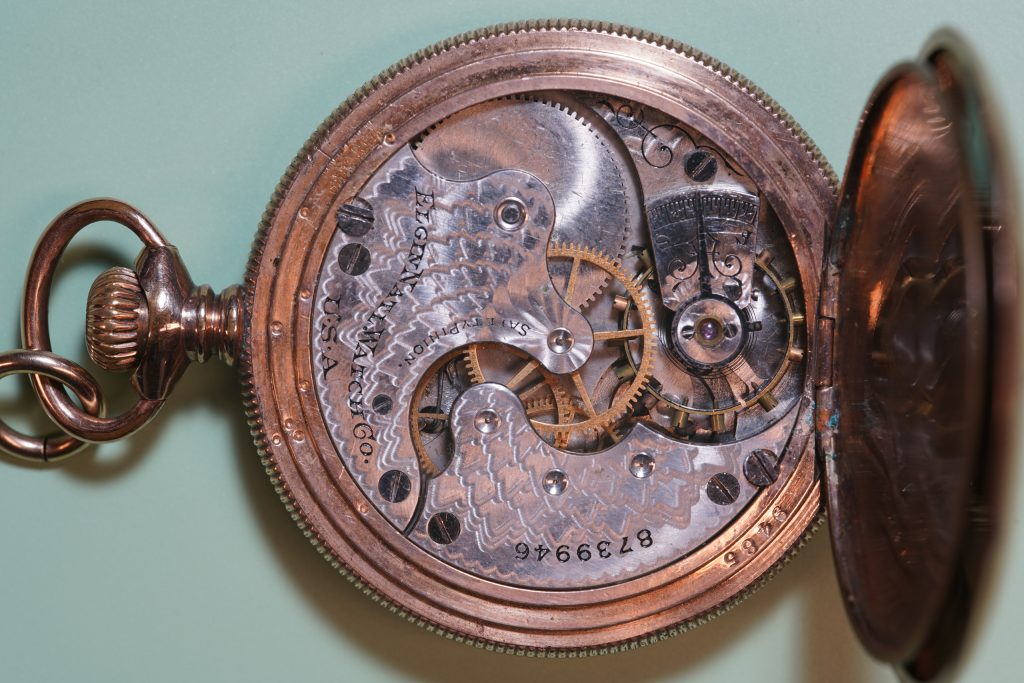
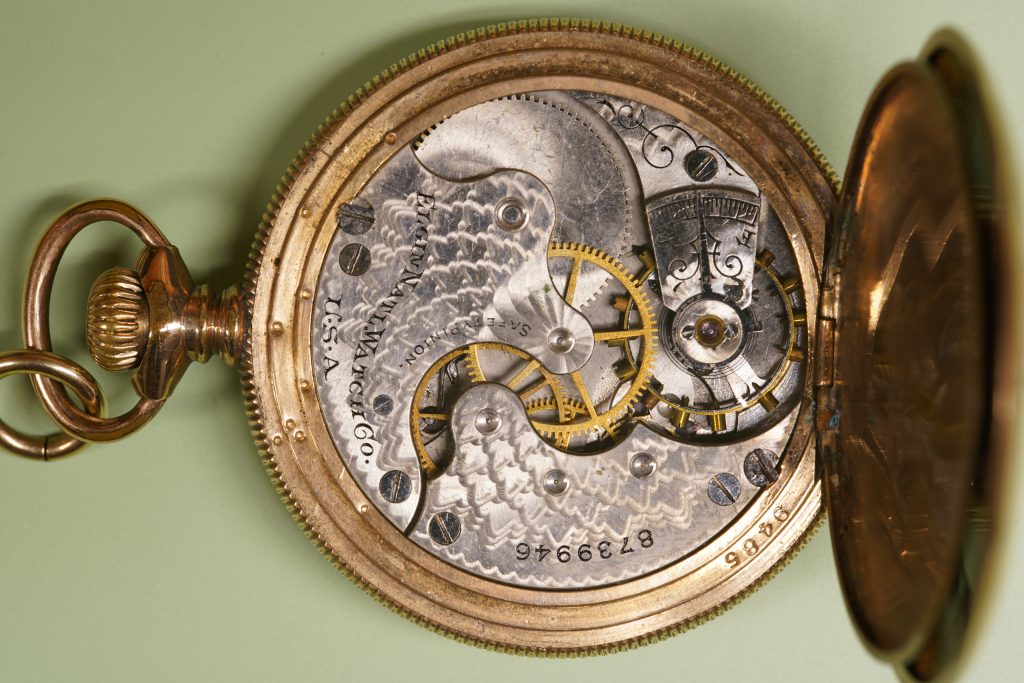
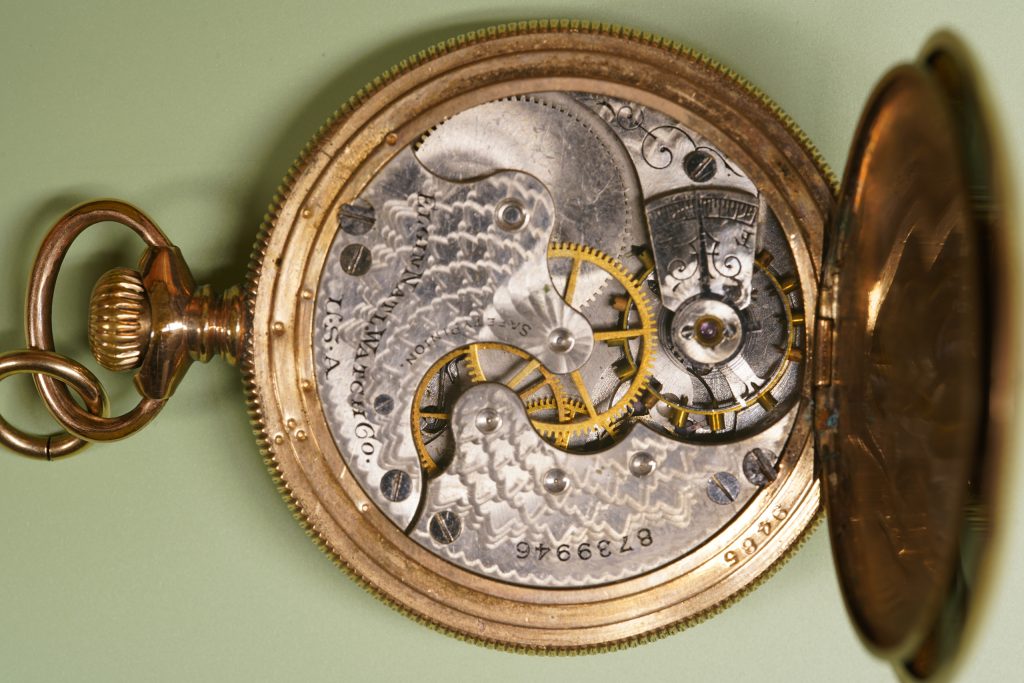
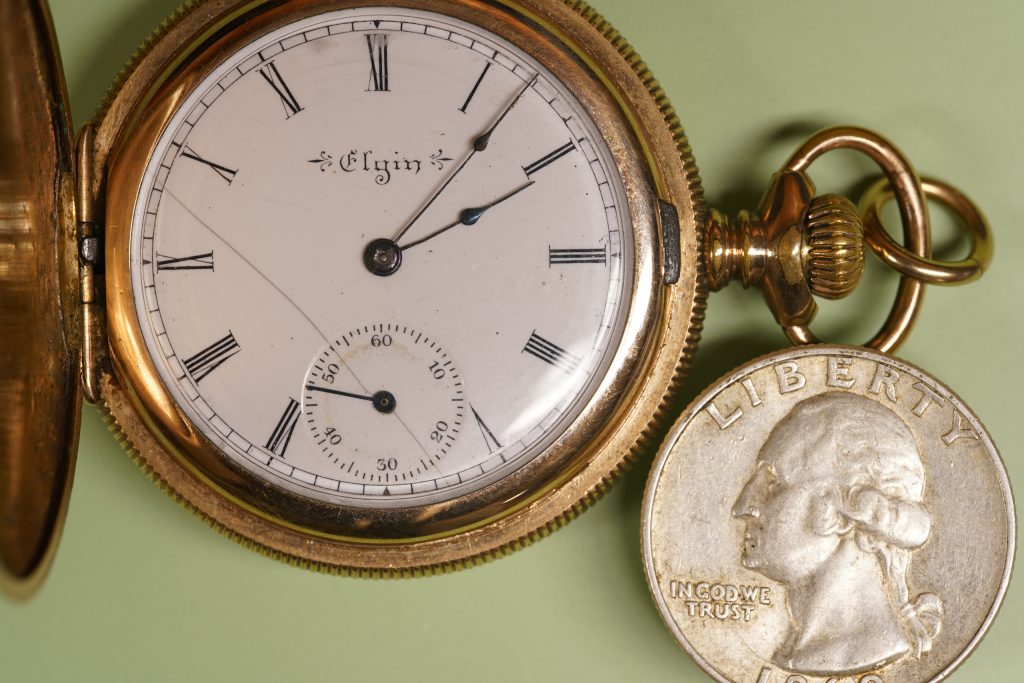
Mainspring
Width: 1.85mm
Length: ~450mm (~18 inches)
Thickness: 0.18mm
Apparently it’s Elgin #824.
Job 6 – Patek Philippe Ladies’ Watch
Watch Model: Patek Philippe
Year Made: ~1932
Movement Model: Patek Philippe #949478, 7-70
Case Number: Ref. 3006, #697379
Mass, case+movement: 9.7g
Mass, movement alone: __g
Dimensions, case: 18.46mm diameter x 7.10mm thick
Crystal diameter:
Dimensions, movement: 11.9mm wide x ~16mm high x __mm thick
Case Number
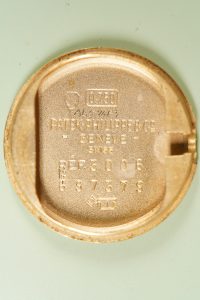
Movement Number
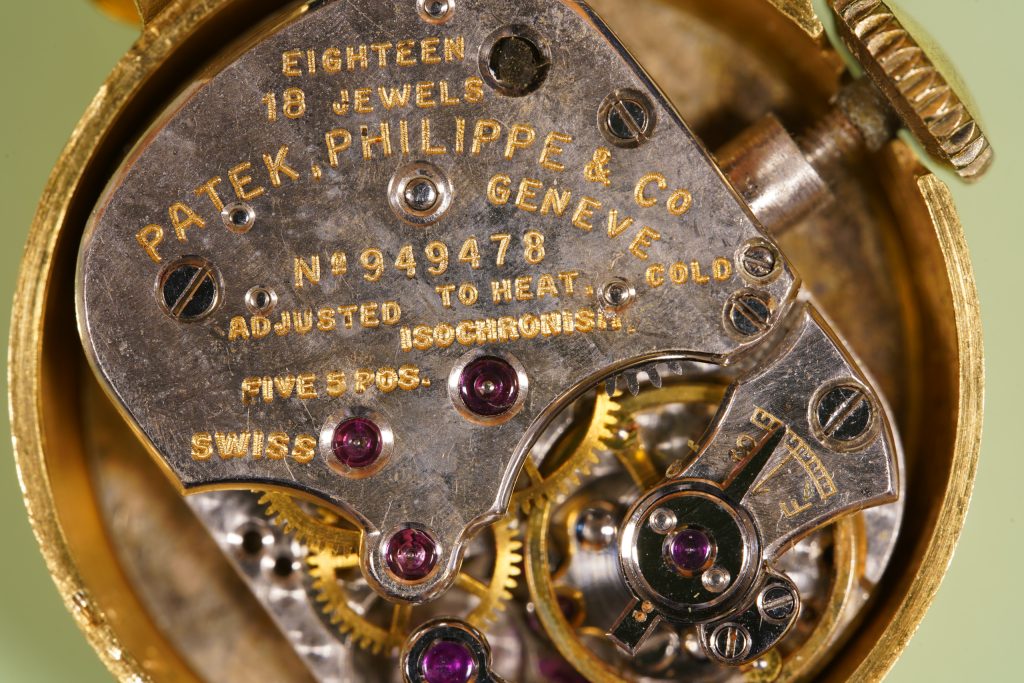
Mainspring
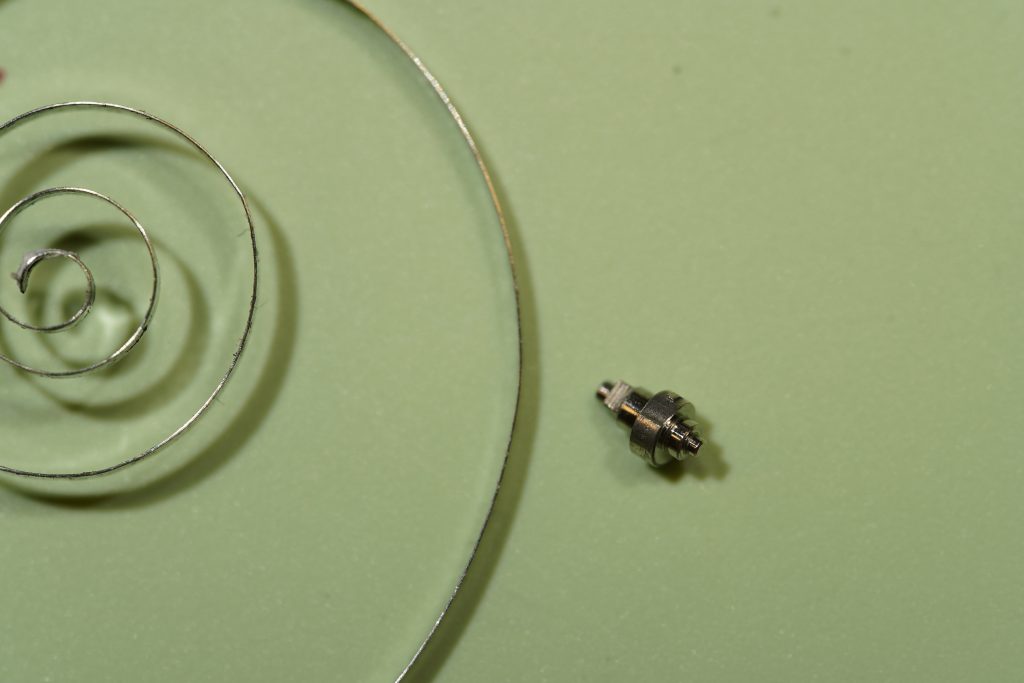
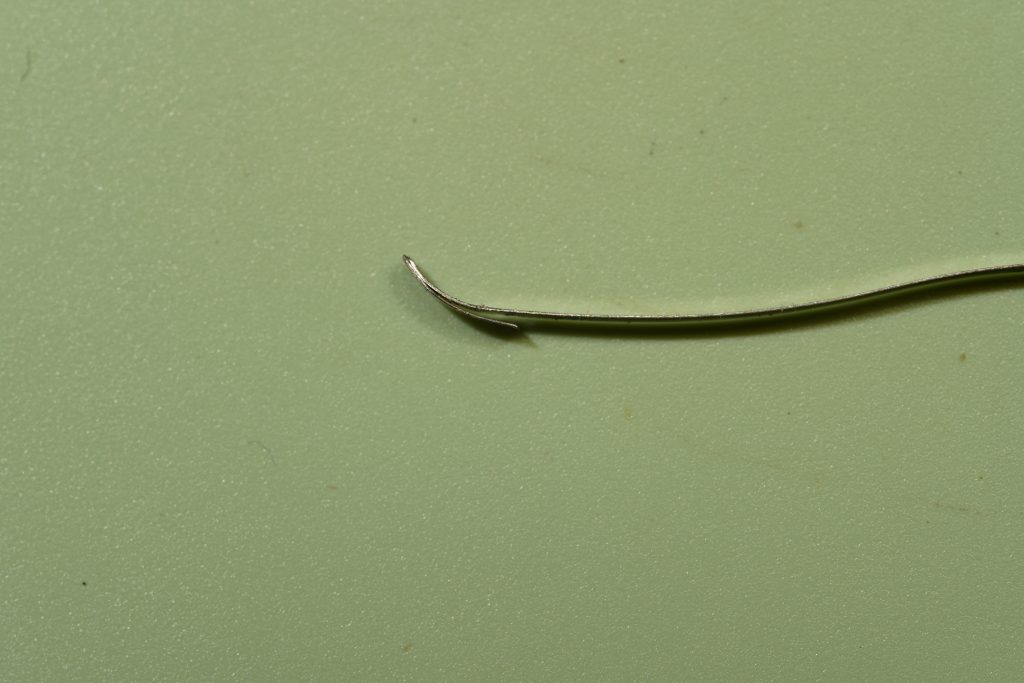
Photos
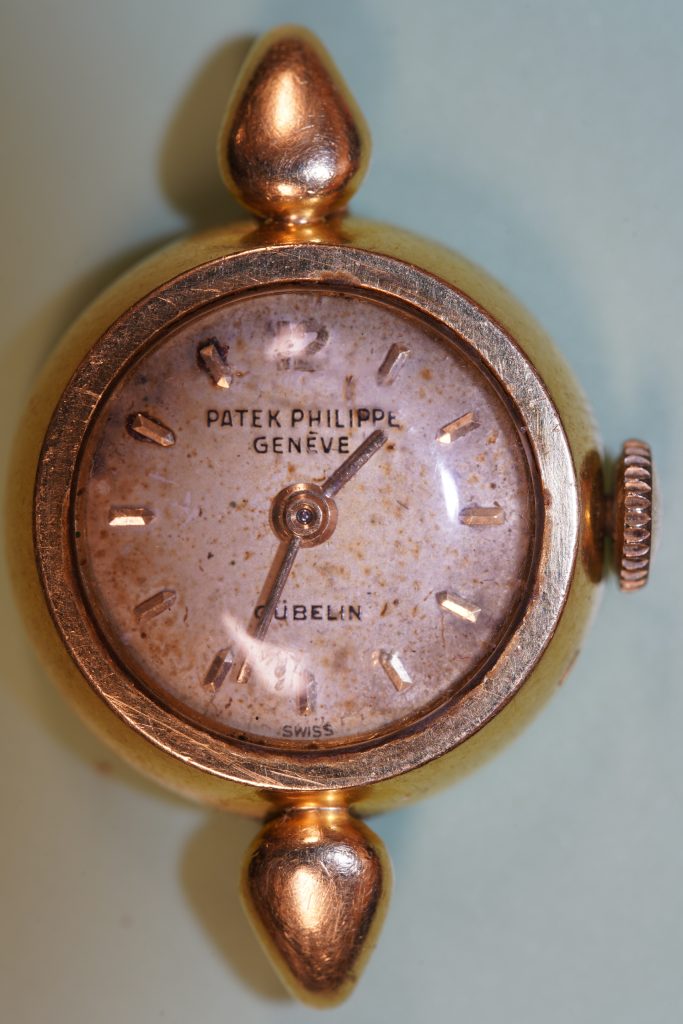
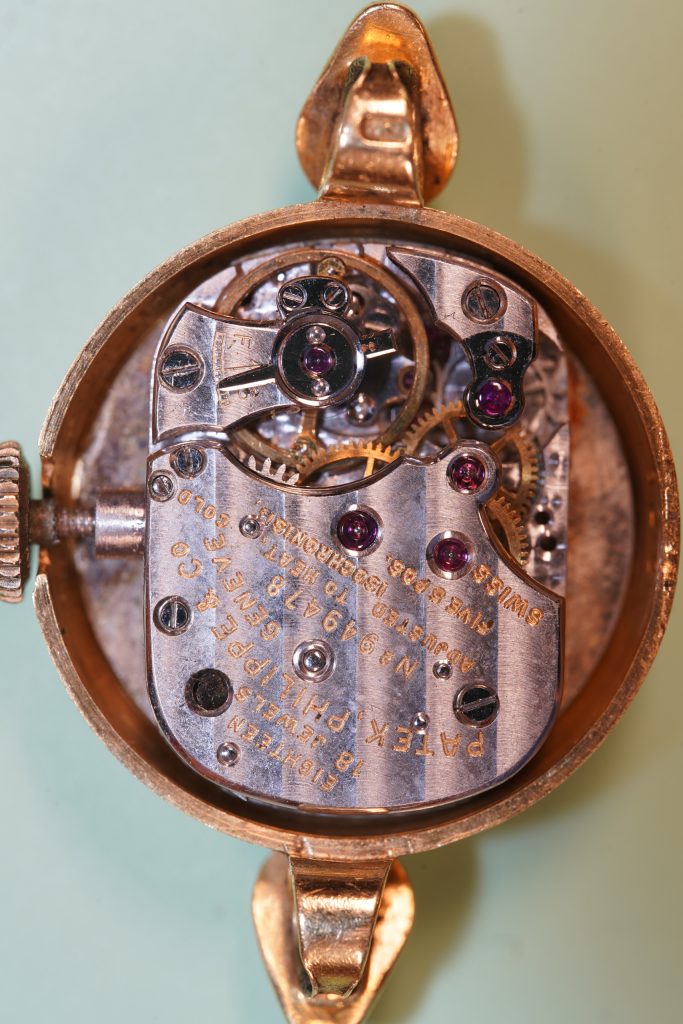
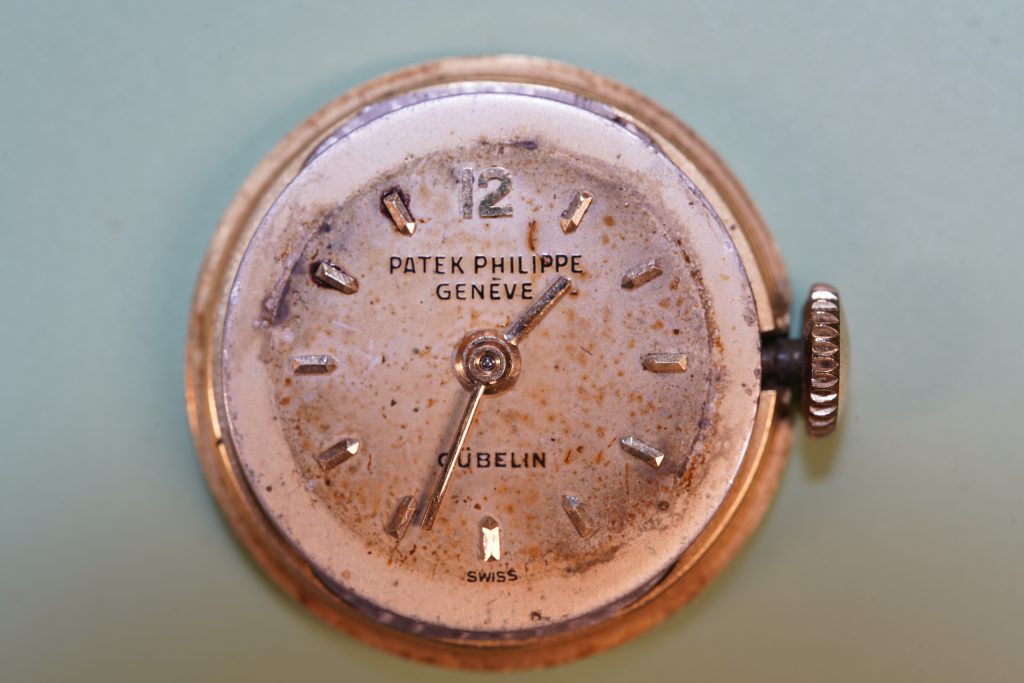
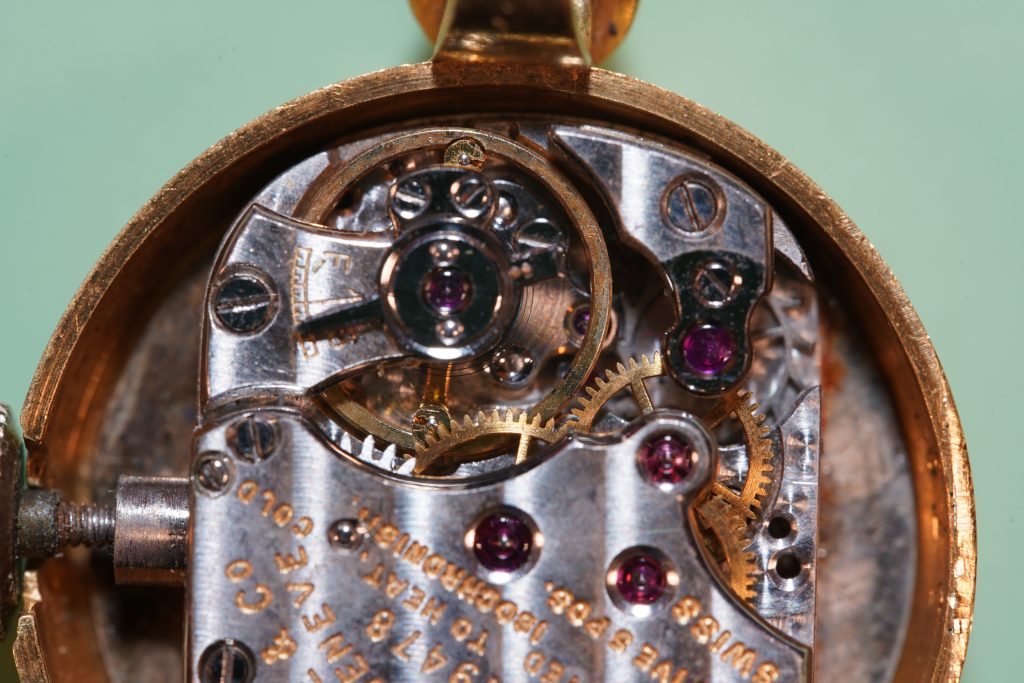
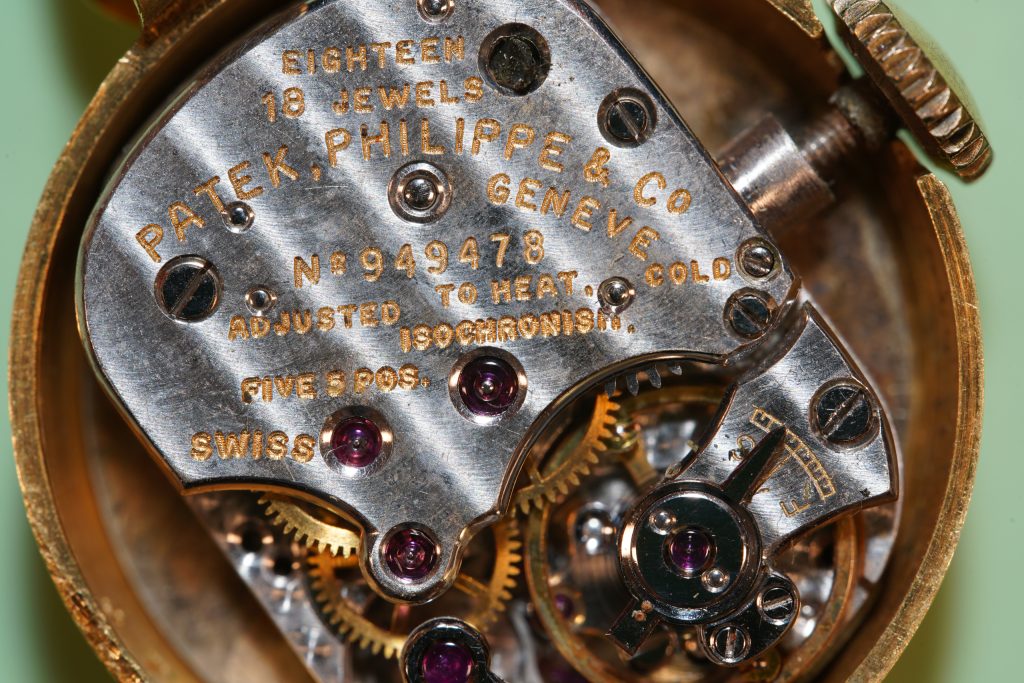
Cannon Pinion Removal with Horotec Watch Hand Removing Press
Click Spring Screw on Quarter
Job 5 – Traffic Engineering Stopwatch #4 – Attempted
Watch Model: Jules Racine & Co. 1018672
Movement Model: Excelsior Park No 3364R
Year Made: ____
Mass: 79.96g (without string attached)
Outer diameter: 50.3mm
Crystal diameter: 42.75mm, 0.89mm thick
Shock-Resistant:
Disassembly Photos, Pre-Cleaning
Problems List
- Shattered crystal.
- Mainspring.
- Fourth gear broken shaft.
Repair Summary
Not worth repair.
At full-throw of the pallet fork, the pallet stone does not clear the ratchet wheel tooth:
After mainspring replacement, the watch ticked through two or three teeth of the ratchet wheel, then get stuck. Normally, I would look into adjusting the ratchet wheel or pallet fork, but since the case was bent and the crystal shattered, I believe the entire movement was slightly warped throughout. When resassembling, the bridge holes didn’t quite line up, further indicating the whole movement is bent.
Job 4 – Seiko Solar Crystal Face – Fixed
Broken crystal face:
Replaced:
Job 3 – Plasma Cutter – Attempted
Customer brought in a plasma cutter that had popped when first powered on then did not power on after that.
I fixed the obviously-damaged arc drive lug, but the device still didn’t power on. It was not worth troubleshooting the rest of the device at the time as it is difficult to disassemble. No charge to the customer, but I probably should have checked the primary power section of the cutter first.
I didn’t take a picture of the final solder
The customer still has it. I may try troubleshooting again sometime …
Job 2 – Seiko Bell-Matic Secondary Crown – Fixed
Missing secondary crown:
Replaced: